What is Porosity in Welding: Recognizing Its Causes and Enhancing Your Skills
What is Porosity in Welding: Recognizing Its Causes and Enhancing Your Skills
Blog Article
Untangling the Mystery of Porosity in Welding: Tips for Reducing Issues and Making Best Use Of Quality
In the elaborate world of welding, porosity continues to be a persistent challenge that can significantly affect the top quality and honesty of welded joints. Recognizing the aspects that add to porosity formation is important in the search of flawless welds. By deciphering the mystery of porosity and executing efficient methods for flaw reduction, welders can raise the requirements of their job to attain premium top quality end results. As we explore the midsts of porosity in welding, discovering the tricks to its prevention and control will be paramount for professionals looking for to understand the art of high-grade weldments.
Comprehending Porosity in Welding
Porosity in welding, a common concern experienced by welders, describes the existence of gas pockets or voids in the bonded material, which can endanger the stability and quality of the weld. These gas pockets are normally caught throughout the welding process as a result of different factors such as incorrect shielding gas, polluted base products, or inaccurate welding criteria. The formation of porosity can damage the weld, making it vulnerable to fracturing and rust, inevitably resulting in architectural failures.
By acknowledging the significance of preserving correct gas protecting, making sure the cleanliness of base materials, and enhancing welding settings, welders can substantially minimize the chance of porosity development. Generally, a detailed understanding of porosity in welding is necessary for welders to generate top notch and long lasting welds.

Usual Root Causes Of Porosity
When checking welding processes for potential top quality problems, understanding the usual root causes of porosity is important for keeping weld stability and avoiding structural failings. Porosity, defined by the presence of dental caries or spaces in the weld steel, can substantially compromise the mechanical properties of a welded joint. One usual reason for porosity is improper protecting gas coverage. Insufficient securing gas flow prices or improper gas blends can lead to atmospheric contamination, leading to porosity formation.
An additional widespread reason for porosity is the existence of wetness and impurities on the surface area of the base metal or filler material. When welding materials are not correctly cleaned up or are revealed to high degrees of moisture, the evaporation of these impurities throughout welding can create voids within the weld bead. Additionally, welding at incorrect specifications, such as excessively high travel speeds or currents, can generate extreme disturbance in the weld swimming pool, trapping gases and triggering porosity. By attending to these typical causes with appropriate gas protecting, material preparation, and adherence to optimal website here welding parameters, welders can minimize porosity and boost the top quality of their welds.
Methods for Porosity Prevention
Implementing reliable preventative steps is essential in minimizing the event of porosity in welding procedures. One technique for porosity avoidance is making sure proper cleansing of the base metal prior to welding. Pollutants such as oil, oil, rust, and paint can lead to porosity, so detailed helpful resources cleansing using proper solvents or mechanical methods is crucial.

One more key safety net is the option of the best welding consumables. Making use of premium filler products and shielding gases that appropriate for the base metal and welding procedure can significantly minimize the threat of porosity. Additionally, keeping proper welding specifications, such as voltage, current, travel rate, and gas flow rate, is essential for porosity prevention. Differing the recommended settings can lead to improper gas protection and poor fusion, causing porosity.
In addition, employing proper welding methods, such as keeping a regular travel speed, electrode angle, and arc length, can aid protect against porosity (What is Porosity). Sufficient training of welders to ensure they follow best practices and quality assurance procedures is also important in reducing porosity problems in welding

Ideal Practices for High Quality Welds
Making sure adherence to market standards and correct weld joint prep work are essential aspects of achieving continually high-grade welds. Along with these foundational actions, there are a number of best techniques that welders can apply to additionally enhance the top quality of their welds. One secret practice is keeping appropriate cleanliness in the welding location. Pollutants such as oil, oil, corrosion, and paint can adversely influence the high quality of the weld, leading to issues. Completely cleansing the workpiece and bordering area prior to welding can help minimize these problems.
An additional best method is to carefully choose the ideal welding parameters for the details materials being joined. This consists of establishing the appropriate voltage, existing, take a a fantastic read trip speed, and protecting gas circulation price. Proper specification option guarantees ideal weld infiltration, fusion, and general top quality. Using premium welding consumables, such as electrodes and filler steels, can dramatically influence the final weld quality. Investing in premium consumables can lead to more powerful, a lot more sturdy welds with less defects. By following these best methods, welders can regularly create premium welds that satisfy market requirements and surpass customer expectations.
Relevance of Porosity Control
Porosity control plays an essential role in making certain the honesty and high quality of welding joints. Porosity, characterized by the visibility of tooth cavities or voids within the weld steel, can dramatically jeopardize the mechanical buildings and architectural integrity of the weld. Too much porosity compromises the weld, making it a lot more vulnerable to fracturing, rust, and overall failing under operational tons.
Efficient porosity control is crucial for maintaining the preferred mechanical properties, such as stamina, ductility, and durability, of the bonded joint. What is Porosity. By minimizing porosity, welders can improve the general top quality and reliability of the weld, making sure that it fulfills the efficiency needs of the intended application
Additionally, porosity control is crucial for attaining the wanted visual look of the weld. Excessive porosity not just compromises the weld however likewise interferes with its aesthetic charm, which can be essential in industries where aesthetic appeals are crucial. Correct porosity control strategies, such as making use of the right securing gas, managing the welding specifications, and making sure appropriate tidiness of the base materials, are vital for producing top quality welds with minimal defects.
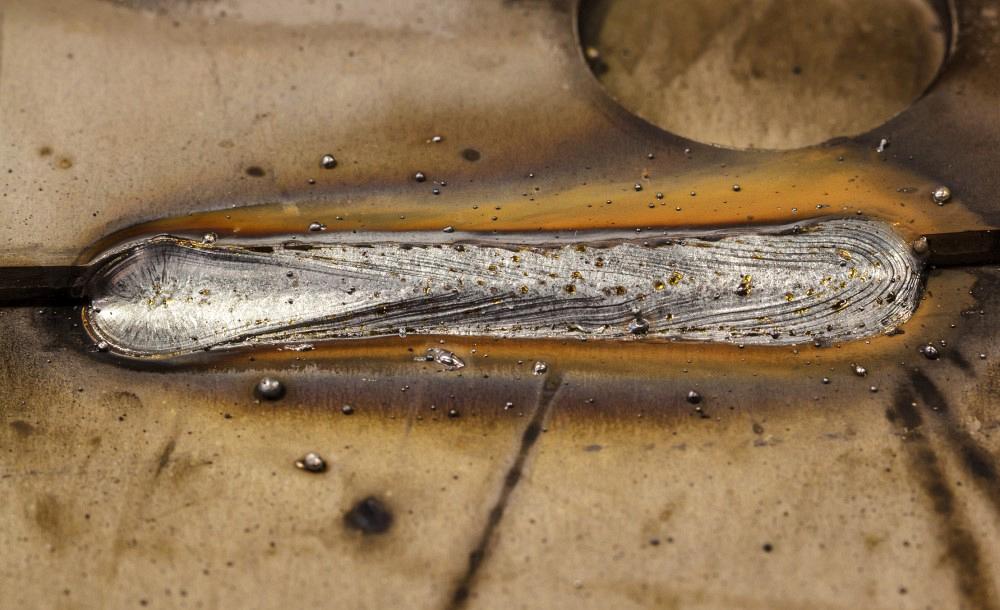
Conclusion
In final thought, porosity in welding is a common flaw that can compromise the high quality of the weld. It is important to regulate porosity in welding to ensure the honesty and strength of the final item.
Report this page